Formlabs large IPA wash.
Wash Tank concept for Form 3L
2017
Internship at Formlabs
Formlabs is a Somerville, MA based 3D printer manufacturer. They make SLA and SLS based 3D printers and is one of the leaders in the additive manufacturing industry. For my internship there I worked on an IPA wash station for Form 3L. The button below leads to the formlabs
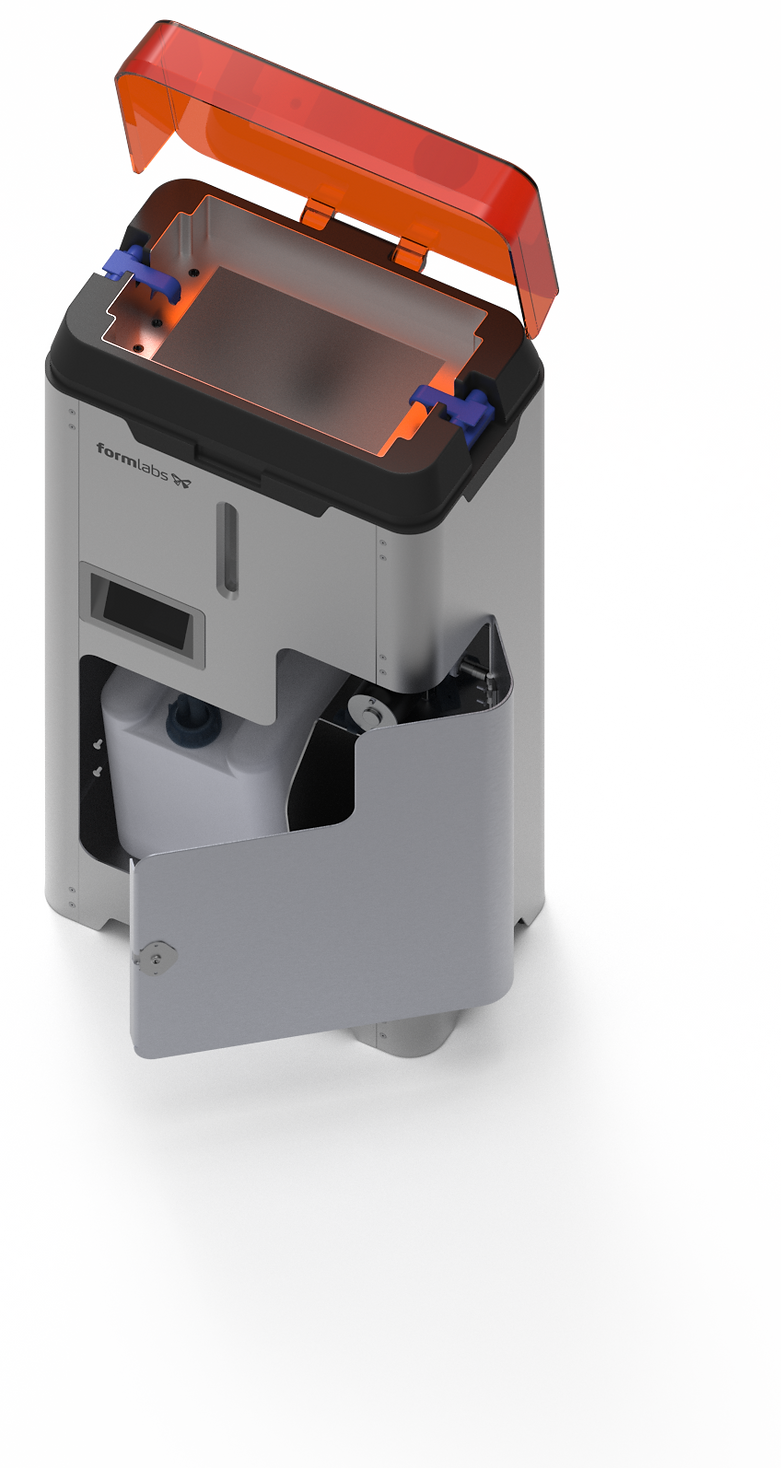

Concept rendering
Imagined production version.




Works-like prototype
Documentation on making the initial prototype.

The wash system Formlabs used to wash larger SLA parts at the time (picture on the left) is a fairly simple setup that uses a fuel pump to transfer the IPA from the reservoir to the wash tank. The fuel pump also serves as an agitator. I am tasked to figure out the direction the future production model will take. There are several important issues my design should address:
- Ensures Safety during operation with large quantities of flammable liquids.
- Intuitive user experience
- Solid and concise structural design.
- Manufacturability
I decided to reuse some components from the current wash setup. Because IPA is very flammable, many of these parts must be either UN certified or spark proof to be used with IPA. The final housing design should also be spark-proof to ensure safety.

Timer

Valves

Explosive proof pump

IPA wash tank

IPA reservoir
I came up with two potential layouts to build the wash machine. The first setup requires fewer parts while the second setup requires multiple valves, but would result in overall better user experience.




VS






Few possible layouts for both single reservoir and double reservoir system.
Single reservoir.

Double reservoir.

Ultimately, single reservoir system is chosen for it's simplicity. A foam core model is made to test the ergonomics.


Another component that needs to be addressed is the sealing system for the container. Because the IPA reservoir needs to be taken out of the machine occasionally for refilling, a removable sealing lid must be implemented into the design for better refilling experience. Below are some initial sketches.
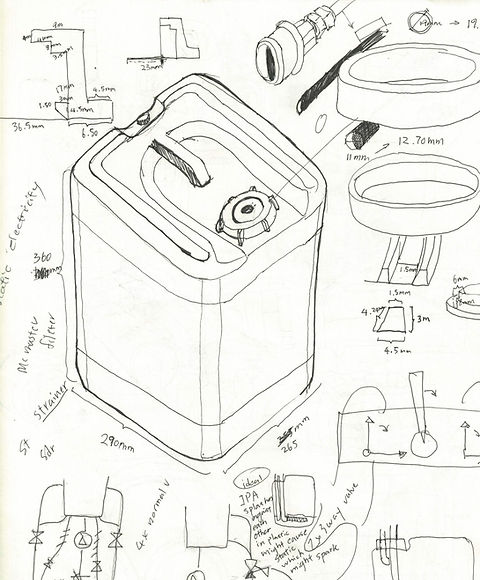



I printed several iteration of the lid. The final design has 3 parts and sandwiches all the parts together once the cap is tighten.
O-ring 1

Patty
O-ring 2
Cap
Tank insert


The next step is to design a pipping layout. The optimal layout would be one that allows IPA to flow easily without leak, and take up as less space as possible.

These pipping would be connected to a stainless steel sink. The pipping allows the overflowing IPA flow back to reservoir. A layer of silicone is sandwiched in between the lip and the sink for sealing.

Working prototype.
The prototype has a wooden frame for simple adjustment.
Assembling.
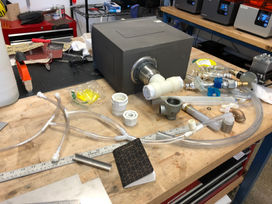
Demonstration video.
Video shows how the prototype pump IPA (in this case water) from the reservoir to the wash tank.
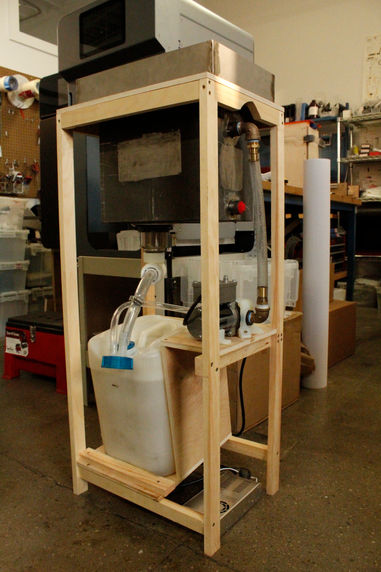
Sketches.
The final production version would have a sheet metal housing, here are some of my initial sketches.

Thank you
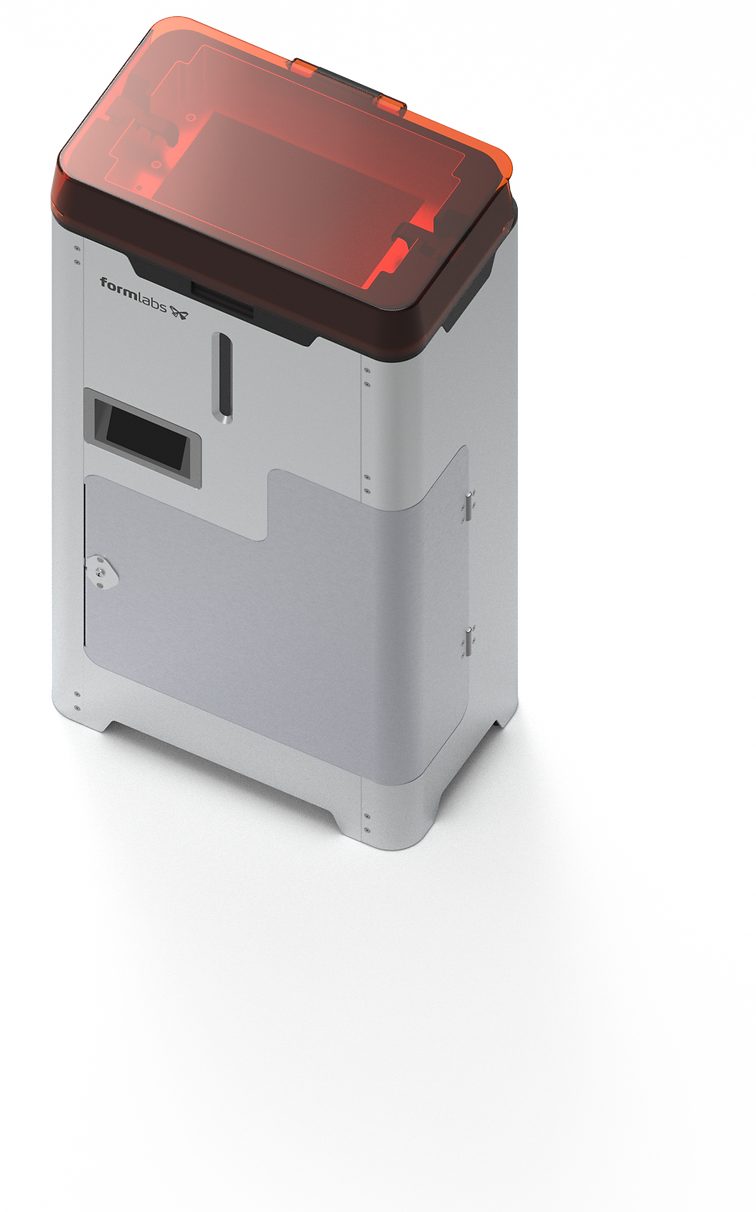